Ski Boot Flex: The Facts!
- Admin SOLE Sports
- Feb 4, 2021
- 5 min read
It seems to be a regular "Mistake" "Chinese Whisper" when it comes to ski boot flex ratings. Like many of you here, over many years and by many people i have heard that "X's 100 flex" isn't the same as "Y's flex." and whilst you may try on two different boots by different brands in a ski shop and feel a stark difference between said "Flex", this isn't because a brand's flex is different to anothers, more precisely two different boots from the same brand may feel different in the store. Here is why and how you feel the differences, but rest assured the machines, the tests are carried out in the same way across all brands, it would be hilarious to see them do different tests and get so close to the other's and just stick some number relative to a feel, albeit not exact and yeld a pretty close result.
So firstly the tests are carried out in the same way, using similar bespoke tools by all brands, again i stress i have, like many of you heard that's not the case, however I have had a play with many of these machines, and with the exception of maybe 3-4 brands they all are done the same. Those i've not seen would I expect to test identically, the chance that those that i haven't seen, doing things different would just be too much of a coincidence so I will assume, rightly or wrongly that to be the case.
Firstly the test is conducted to define the longevity of the boots, as well as many other things, such as your "flex rating" resistance and "flex pattern" smooth and progressive, however these results are just data after the fact, the lifespan of the "flex" is what's being tested.
So the test box is set to a temperature that is optimum for the plastics 22°c, it seems odd not to test the boots at the temperatures at which we ski, however the results here at let's say -5°c are simply too inconsitent due to many factors that we'll go into later.
Now that we have the temperature where we need it, the boot is placed inside the box and a false leg/piston is placed inside it. This is the part where most of the inconsisteny is, get the right amount of "fill" and tension on the boot is quite difficult, this is the first part where we may see "false" or untrue data. I can't remember the exact method used here, but if memory serves me right we're looking for the plastic to be under average tension "10nm" resistance to closure. (Not alot basically, but as much as you should theoretically need to close your boots and be secure.)
Ok, so now it gets easier, the boots will be pulled through a range of angles to start, around and upto 20° to calibrate the machine, and find the consistant flex pattern of the boots (where the range of motion is most consistant, when designed correctly from it's start through 10°).
Once calibrated and adjusted to the particular boot, the machine then flexes the boot 30,000 times. We reckon this is the equivalent to around 200 days skiing, depending on the amount of turns done, however temperature and tightness of the buckles, as well as the effects of UVA/B over the lifespan of the boots make this theoretical and almost mute, but we need a number to work with and a test of sorts, so this is the figure.
And that's it, tests done, the machine now gives us a reading and a whole bunch of data we can use.
It's important to add at this point that upto this point we only have one mould made, size 26.5 usually they cost a fair amount of cash, upwards of 100k and are often binned several times before we're fixed on it's production and the other sizes are made. This is again a slight problem, as smaller sizes may then keep certain dimensions and bigger ones too, delta angles are sometimes considered, often not, plastic thickness and relative dimensions heel to toe, heel to shin, can often change these test results too.
Now, let's look at these results, the ones that will designate your 130 nm Flex ski boot. The boot yelded a result of 130nm average between 126-134nm, after being flexed 30,000 times and the average resistance was 130nm. Total Energy divided by 30,000.
There are permitted margins. If a boot tests between 126nm and 134 NM it's stamped 130nm.
Thank feck for that, if they published exact results, you'd be coming to buy boots and trying 134,135,136,137,138nm it would be hell and carrying stock impossible, so, it's rounded up/down as needed for commercial reasons.
So, why do we have such varied feelings instore with these diffent models or brands??
Well firstly, as above, you could be testing a real 126nm or a 134nm and both would be classed 130nm
Ok, if you'll follow me here.
First let's take two identical boots, one black, one white. Same brand!
Room/Store temperature is assumed to be 27°c, let's agree it is. 5°c warmer than the environment at which the boots are tested.
So already at this temperature the boots are softer than tested, in a cold shop, like ours often is say 20°c the boots are stiffer.
Now, our white boot flexes less than our black boot, simple. The black boot absorbing more heat more quickly, the white reflecting, resisting it.
So, two identical boots of different colour yeld different results.
Now, let's keep the 130nm flex boots, keep them black and white and make the white one a high volume/wide boot and the black one, low volume/narrow. The two boots have exactly the same thickness of plastic, they are identical except colour and shape. Same brand!
Now you will put your feet in the two boots, let's assume they are totally symetrical.
The white boot is too loose, so you buckle it up tighter, the black one a little to tight, so you buckle it up less.
Now, the black boot is both looser and softer due to temperature.
The White boot stiffer as it's white, but also, because you do it up tighter you remove alot of the inherant elasticity of the plastic, stretch it essentially.
The result is it is again stiffer for two reasons.
Now let's mix it up massively.
We keep the white boot, high volume, the black boot, low volume, however, now the black boot has thinner plastic, the white boot is a heavier, thicker plastic. Same plastic, let's say Poly Ether, a fairly stable plastic all said regards ski boot manufacture. There is more stable and many less stable. Same brand!
This adds to the effect of difference in temperature and tension over the buckles.
For the third time our two 130nm boots are subject to variables that effect their results at room temperature.
Now, let's change the final piece of the puzzle.
Change the materials too, a 4th variable and now these things feel different for a fourth reason.
The black boot is narrower, lower volume, thinner and now it's made of Polypropylene. Measuring 126nm
The white boot is wider, higher volume, thicker and made of Nylon/Grilamid. Measuring 134nm
Same brand!
There are now 5 reasons why two boots feel different in a shop, despite both being stamped 130nm.
Now, one last, oops two last points for use on the hill.
Different materials, different thinknesses and different colours react differently at different teperatures.
UVA and UVB will degrade your plastics, freezing temperatures, and blue sky days will damage your boots flex patterns and the results would be different quicker over those 30,000 flexes/200 days.
RECAP!
So, all manufacturers use the same tests.
The same manufacturer may make two boots that feel very different with the same rating in the store.
Conclusion/Correction.
Boots stamped with the same flex may feel different, "DIFFERENT MODELS" may feel different, not different brands, however you may feel a difference between brands, but really it's the "Model" that is different!!!!!!
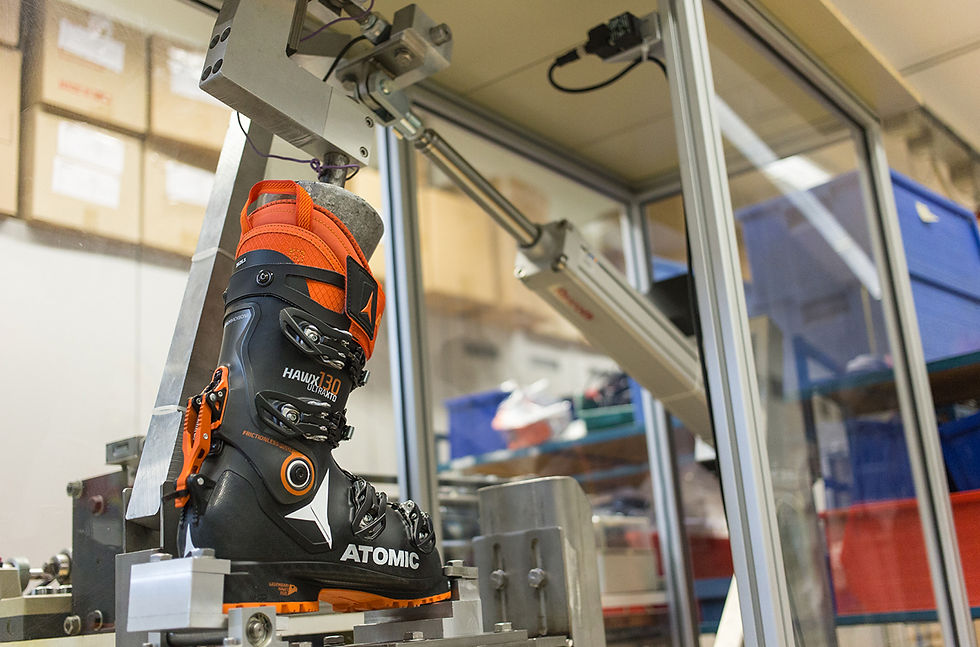
Comments